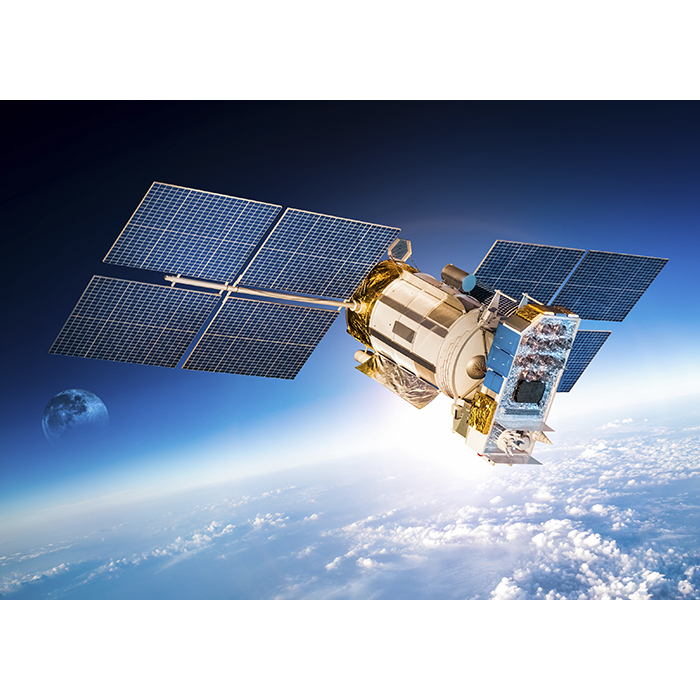
Designing Connectors for Low Earth Orbit
The vast majority of satellites launched, whatever their size, are intended to operate in a low earth orbit (LEO). Some now even orbit Mars. Many components used in LEO satellites are off the-shelf commodities. They are protected from the extremes of space through careful design, but there are some conditions that will present specific challenges, and these must be taken into account when selecting components.
Overcoming Unfamiliar Challenges
Space really is a new frontier and like all pioneers who bravely forge the first pathways, those who venture there must continuously adapt and innovate to overcome unfamiliar challenges. Despite now having several decades of space flight and exploration behind us, there are many examples of new entrants into the sector that will be experiencing it all for the first time.
Take, for example, the huge private investments going into commercializing space right now. This includes tourism, of course, but in the immediate timeframe it comprises greater diversity in satellites, in terms of size, function and expected lifetime. It is now easier and cheaper than it has ever been to put artificial objects into orbit around our planet, and an increasing number of services are being created to take advantage of that.
These are complex systems that need to be optimized for size and weight to keep costs as low as possible. But they are still systems, built using components that need to be assembled and connected. Momentum has been building behind the ‘satellite on a chip’ concept for many years but it has yet to be realized. However, the size of satellites continues to reduce, with micro-satellites, nano-satellites, pico-satellites and even femto-satellites. But even the examples of the very smallest device still comprise multiple components. A satellite with just two components will still need some form of interconnect. This means connectors designed for space are a critical part of the overall system.
The vast majority of satellites launched, whatever their size, are intended to operate in a low earth orbit (LEO). Some now even orbit Mars. The point here is that while they are not contending with the harshness of deep space, they are still exposed to an environment unlike any on the surface. An object in LEO makes in excess of 11,000 orbits of Earth per day, in conditions that would challenge any object. Despite this, many components used in LEO satellites are off-the-shelf commodities. They are protected from the extremes of space through careful design, but there are some conditions that will present specific challenges, and these must be taken into account when selecting components.
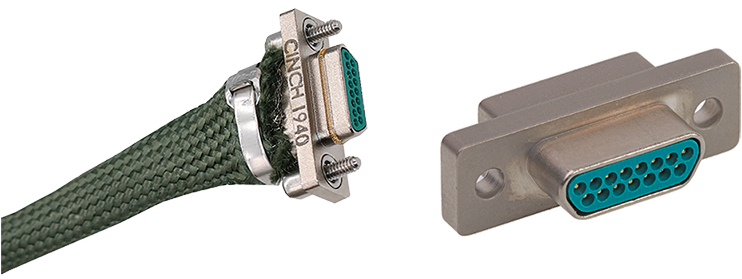
Dura-Con MIL-DTL-83513 connectors and assemblies have been utilised in space applications since the 1970s
Dura-Con Solutions for Rugged Applications
View Product VideoThe Vacuum of Space
The extremely low pressures created by the vacuum of space causes any vapor captured in a material to be expelled. This process, known as outgassing, can also release compounds into an enclosed area, such as inside a satellite. These compounds can present a threat if they are volatile or react to other compounds in a volatile way.
Outgassing can lead to damage or failure, if vapors collect on the surface of critical components such as sensors or photovoltaic materials. Vapors may also collect in a way that creates a short-circuit between components, connectors or leads.
It follows that outgassing is taken extremely seriously. NASA maintains a database of materials that records their outgassing characteristics in terms of Total Mass Loss (TML %) and Collected Volatile Condensable Materials (CVCM %). The ASTM (American Society for Testing and Materials) standards E1559 (Test Method for Contamination of Outgassing Characteristics of Spacecraft Materials) and E595 (Test Method for Total Mass Loss and Collected Volatiles Condensable Materials from Outgassing in a Vacuum Environment) define the methods for measurement.
NASA issued the space station external contamination requirement SSP 30426, which defines the limits for molecular deposition and the release of particulates. In order to comply, materials should meet a TML of 1.0% and/or CVCM of 0.1%. Those materials prone to outgassing are often chemically derived, such as composites. These materials are common in the design of connectors, because they also exhibit good resistance, making them ideal electrical insulators. Connector manufacturers intending to qualify their products for use in space flight must demonstrate compliance with these standards.
Aggressive Oxygen
Any material in space may find itself exposed to the aggressive oxidizer, Atomic Oxygen (AO). This is formed when oxygen reacts with UV radiation. The single atoms in oxygen bond with molecules. In our atmosphere the reaction is not sustained, but in space the abundance of UV radiation makes it much more sustainable. In an LEO, 96% of the oxygen present occurs in atomic form.
Metals and plastics can be affected by the presence of AO. In particular, AO effects any polymer containing carbon, nitrogen, sulphur of hydrogen bonds. If fluorine is used in the polymer, the reaction increases with prolonged exposure to AO.
PTFE, which is commonly used as the insulator for electrical wire, reacts when AO is present and exposed to UV. Wires with ETFE insulation are preferred in space applications, as they have good dielectric properties and it is resistant to thermal variations. However, as sunlight is a great source of UV radiation, ETFE-coated wires should not be exposed to sunlight in an LEO application. Connector manufacturers need to develop solutions that can provide some protection against the presence of AO.
The Threat of UV Radiation
Because there is no atmosphere to protect against the sun’s UV radiation in space, its effects are much more extreme. It is particularly damaging to plastics, such as those used as insulators in connectors.
Exposure to UV radiation can affect polymers, changing their mechanical structure. This can manifest as hardening (cross-linking) or weakening (chain scission). Additives may be introduced to the polymer to reduce the effects, but generally the use of connectors in areas that are exposed to UV radiation should be minimised in LEO applications.
Other Extremes
The variations in temperature found in space are much more extreme than those found on the earth’s surface. Again, it is due to the lack of diffusing atmosphere and whether the object is exposed or hidden from the sun’s radiation. If the object experiences both, due to its orbit, the temperature variation will be dependent on the thermal absorption or radiation properties of the material, but could be in excess of 200 °C.
An important parameter here is the Coefficient of Thermal Expansion (CTE), which all materials have. The main issue is that not all materials have the same CTE, which means there can be a mismatch between two materials in the same assembly. This can lead to damage caused by the different rates of CTE as the object cycles through temperature extremes.
Charged particle radiation is another threat that exists in space, the main sources being galactic cosmic rays, solar proton events and trapped radiation belts. In general, AO and UV will be the main consideration for component manufacturers, but this illustrates that there are many aspects that must be considered.
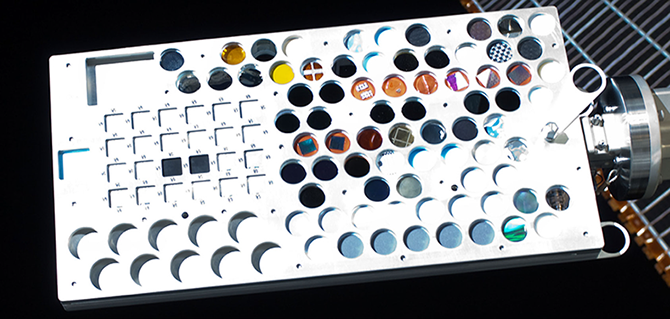
Material testing on the ISS in 2011
Designed for Space
Humans have been sending artificial objects into space for over six decades, so it is not surprising that there are many components that are now considered to be space-ready. In the 1970s NASA developed its Technology Readiness Levels (TRLs), with components being graded from 1 to 9. A grade of TRL 9 indicates the highest level of technology maturity, defined as being ‘fight proven’ in successful missions. The European Space Agency has also been using TRL since 2008, with its own slightly different but very similar definitions for each of the nine levels.
There is a legacy of meeting the needs of the most demanding applications within Cinch Connectivity Solutions. Its CIN::APSE solderless interconnect technology is qualified as TRL 9, for example. The company started supplying the space industry in the 1970s and has continued to do so every decade since. It is already working on solutions for missions that are scheduled for beyond the 2020s.
Its expertise covers all areas of the industry, from LEO satellites, those in geosynchronous orbit and in medium earth orbit (MEO), as well as ground support system and launchers. This includes D-shaped MIL-DTL-83513 connectors, MIL-DTL-1553B solutions and QPS (Qualified Parts for Space) components including RF attenuators.
As well as being a key supplier to NASA missions, Cinch has helped enable the Emirates Mars Mission, the Parker Solar Probe and the One Web project. In LEO applications, Cinch provides components for observation, communication, reconnaissance and surveillance applications, as well as systems designed for navigation and telecommunications.
Harsh Environments and the Need for Quality Sourcing
Designing for LEO can require systems to last in excess of 30 years. In the case of smaller satellites, that may be without any maintenance. Ensuring the components selected can withstand the harsh environment for prolonged periods, from AO to UV and thermal extremes, is paramount to mission success.
Recent developments indicate that we are still only at the beginning of space exploration. The pace of development is accelerating thanks to private investment and an overall increase in demand for the benefits found in LEO applications.
More manufacturers now see the value in developing a supply chain comprised of companies that can demonstrate a long heritage in delivering excellence in this area. For over 100 years, Cinch Connectivity Solutions has manufactured high quality and reliable high-performance connectors and cable assemblies. Cinch is recognized as a world class connectivity supplier of RF, fiber optic, hybrid, microwave components, circular, d-subminiatures, modular rectangular, electronic enclosures and cable assemblies.
Cinch provides innovative solutions to the military, commercial aerospace, networking, telecommunication, test and measurement, oil and gas and other harsh environment industries. At the Bel family of solutions, we aim to exceed our customers’ expectations and continually offer innovative solutions to the rapidly changing needs of the markets and customers we serve.
Explore Bel's Variety of Space Solutions
Bel has a proven space pedigree with a history of missions spanning over six decades, from the Voyager, Mariner, and Apollo ventures of the 1970s to embryonic projects with planned launch dates many years from now.