Traditional physical contact fiber optic connectors have proven to be unreliable in harsh environment applications due to their sensitivity to dirt, dust, mud, water, oil and other contaminants. Expanded beam fiber optic connectors offer the solution. This paper explains the benefits of expanded beam over physical contact and demonstrates how expanded beam connectors offer improved reliability in harsh environments.
RELIABLE PERFORMANCE IN CHALLENGING CONDITIONS
Physical contact connectors were originally designed for datacom and telecom systems, operating in benign environments such as telephone exchanges and data centers. As the name suggests, these connectors employ termini containing optical fibers which physically mate together under spring pressure within an alignment sleeve allowing the optical fibers to contact and make the connection. During assembly, the termini are polished using high precision polishing machines to provide the precise end-face geometry and sub-micron finishes necessary to achieve the required optical performance.
In recent years, these same termini have been incorporated into more rugged multi-way connectors in an attempt to provide harsh environment fiber optic connectors for civil and military aerospace, military ground applications, naval systems and offshore environments.
PHYSICAL CONTACT CONNECTORS IN HARSH ENVIRONMENTS
The fundamental drawback of physical contact connectors is that when in an un-mated state, the fiber optic end-face is exposed to the outside environment. Any contaminants present can degrade the sub-micron polished finish on the end-face when mated and can cause the optical performance to deteriorate significantly particularly when in use or in high vibration applications. Often, even the process of attempting to clean the end-face can cause serious damage to the optical fiber, resulting in high attenuation and reducing system integrity.
Figure 1. Typical physical contact plug and receptacle connectors.
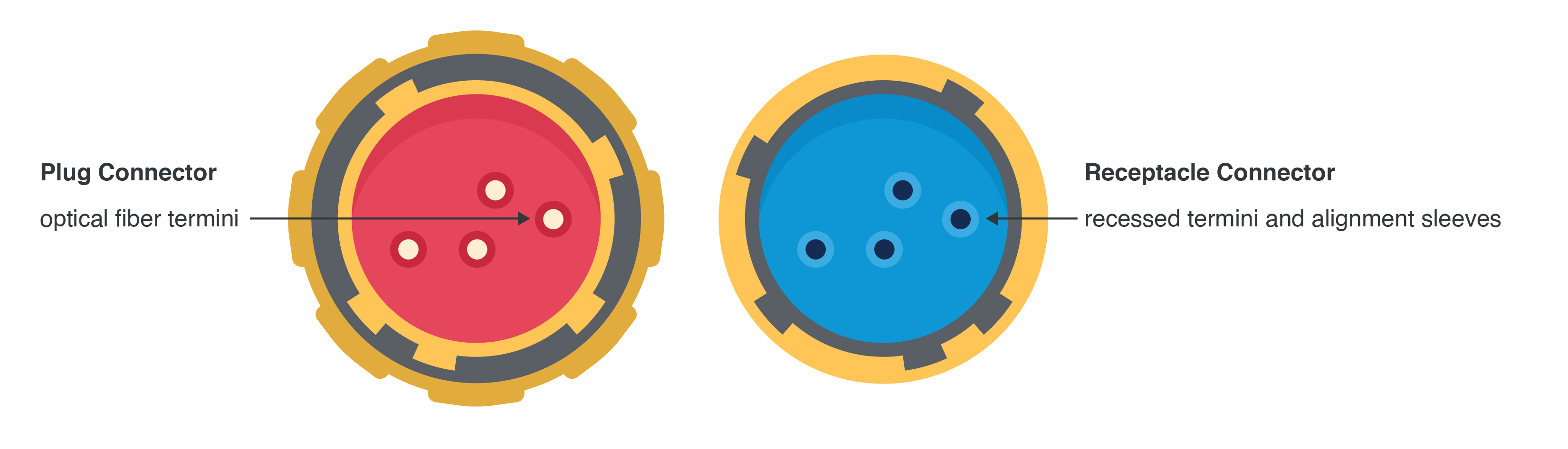
Expanded beam fiber optic connectors have been designed specifically to operate in harsh environments. They utilize a non-contact technique where the fiber is fully sealed behind a lens. The lens effectively enlarges the active area of the fiber, thus providing a connector with greatly reduced dirt sensitivity and therefore higher reliability when used in adverse conditions. The air gap generated between the mated lenses ensures any debris present on the lenses do not cause damage during operation or vibration, providing a further level of ruggedness.
DRAWBACKS OF PHYSICAL CONTACT CONNECTORS IN HARSH ENVIRONMENTS
During a typical fiber termination, the ferrule end-faces are polished on a high precision polishing machine to achieve a radiused profile to allow the mating optical fibers to contact. The mating termini are held in position under spring pressure within a ceramic alignment sleeve. The ferrule end-face geometry and sub-micron polish finish are critical in achieving optimum optical performance.
Figure 2. Physical contact method
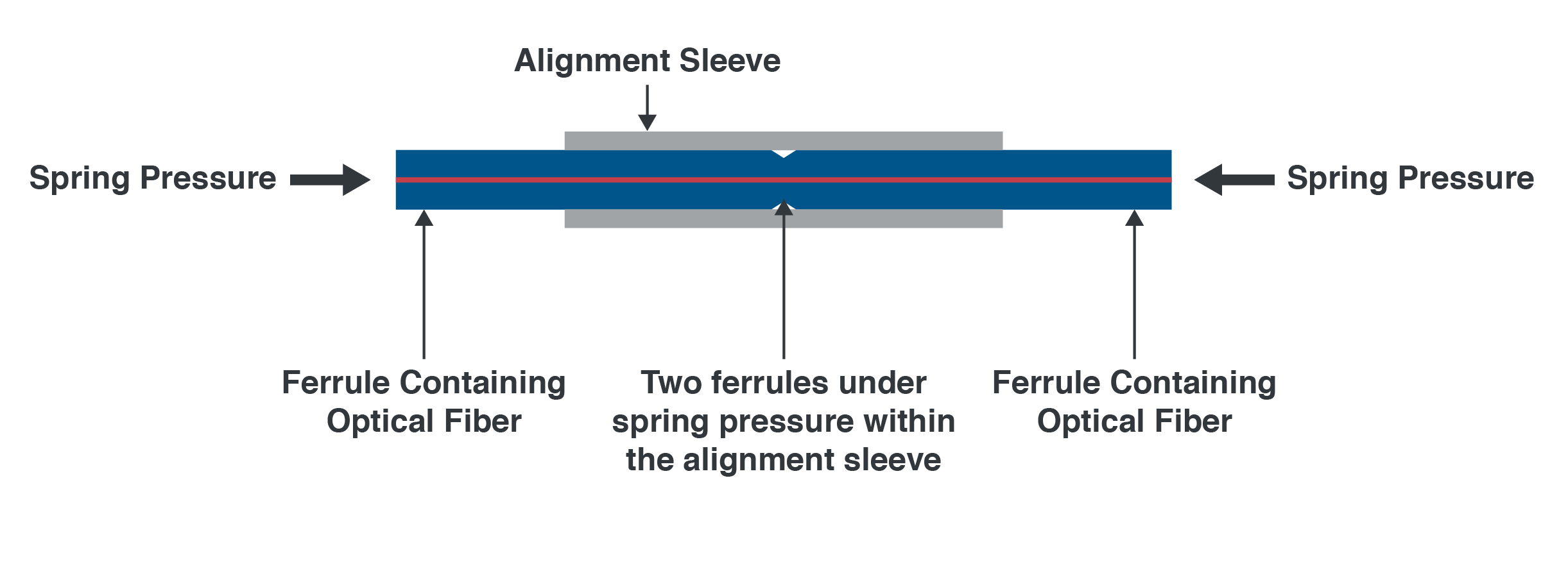
In harsh environments, physical contact connectors have a number of drawbacks:
Contamination: The highly polished ferrule ends are exposed to the outside environment when the connector is in an un-mated state. This allows the fiber to become contaminated with dust, dirt, mud, water, etc. A dust particle as small as Ø9μm on a single-mode fiber core is enough to completely block signal transmission. A typical dust particle size is between Ø5μm and Ø40μm. If a connector with dirty or contaminated termini is mated to another connector, the contamination is passed to those termini in that connector. Moreover, termini with damaged end-faces could permanently damage the mating termini.
Cleaning: Cleaning physical contact connectors is difficult due to there being three components to the connection: two termini and an alignment sleeve. Alignment sleeves are usually retained in the receptacle connector, resulting in the need to clean inside a deep
Figure 3. View on a physical contact termini end-face at 200x magnification showing typical contamination from dust and oily deposits.

narrow cavity. Often, connector disassembly is required to access the termini end-faces and alignment sleeves for cleaning. Special cleaning materials are required to clean physical contact termini. Lint-free tissues, cleaning solvent, and specialist cleaning swabs are essential. Further damage to termini can occur if the incorrect cleaning materials are used.
Water sealing: The termini in physical contact connectors are sprung loaded and therefore inherently difficult to water seal. Some physical contact connectors only seal when mated or if a protective cap is fitted.
Degradation: When in perfect condition, physical contact connectors give good optical performance, insertion loss of around -0.3dB and reflectance in excess of -45dB. However, the optical performance will degrade during normal usage in harsh environments and continue to degrade over the product life. High loss or complete signal failure can occur if the fiber core is damaged.
For physical contact connectors an end-face inspection microscope is essential to check for contamination or damage.
MAINTENANCE CHALLENGES OF PHYSICAL CONTACT CONNECTORS
While physical contact connectors have lower insertion loss than expanded beam connectors when the product is in perfect condition, their optical performance will constantly degrade over the product life eventually leading to signal failure.
Regular maintenance of physical contact connectors is required to maintain good optical performance. This can involve disassembling the female connector parts, removing alignment sleeves (small parts which are easily lost in field conditions) and the use of special cleaning swabs, solvents, and tools (including an end-face inspection microscope).
The servicing of physical contact connectors can only be performed by specially trained technicians. If the termini have been damaged, cleaning will not restore original optical performance. Damaged termini end-faces will require re-polishing and although this can be achieved in the field, it is preferred to carry this out in a clean room environment under workshop conditions. Connectors with severely damaged termini will require complete re-termination or replacement.
While physical contact connectors require specialized servicing and maintenance, expanded beam connectors offer a more reliable and low-maintenance solution for harsh environments.
THE EXPANDED BEAM PRINCIPLE
Expanded beam fiber optic connectors utilize a lens to expand and collimate the light emitting from an optical fiber.
This collimated light beam is transmitted through an air gap to a mating connector, where the light is collected and focused by a second lens into a second optical fiber to complete the connection.
Figure 4. Diagram of expanded beam components and operation.
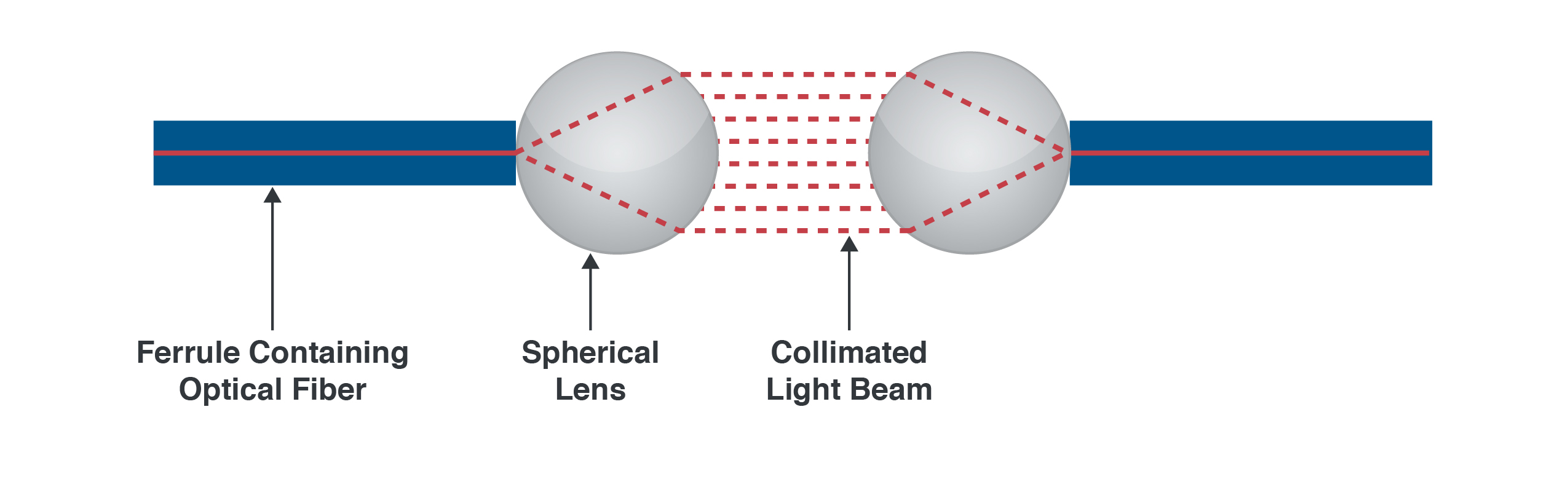
With 50/125 multimode fiber, the expanded and collimated light beam has an active area of around 150 times larger than the original optical fiber core. In single mode expanded beam connectors the active area of the light beam is approximately 2000 times larger.
The effect of collimating and greatly increasing the beam diameter, means that the connector is less sensitive to small particles of dust or other contamination which could completely obscure transmission in physical contact type connectors.
Figure 5. Comparison of EB core size to other fiber types and dust particles.
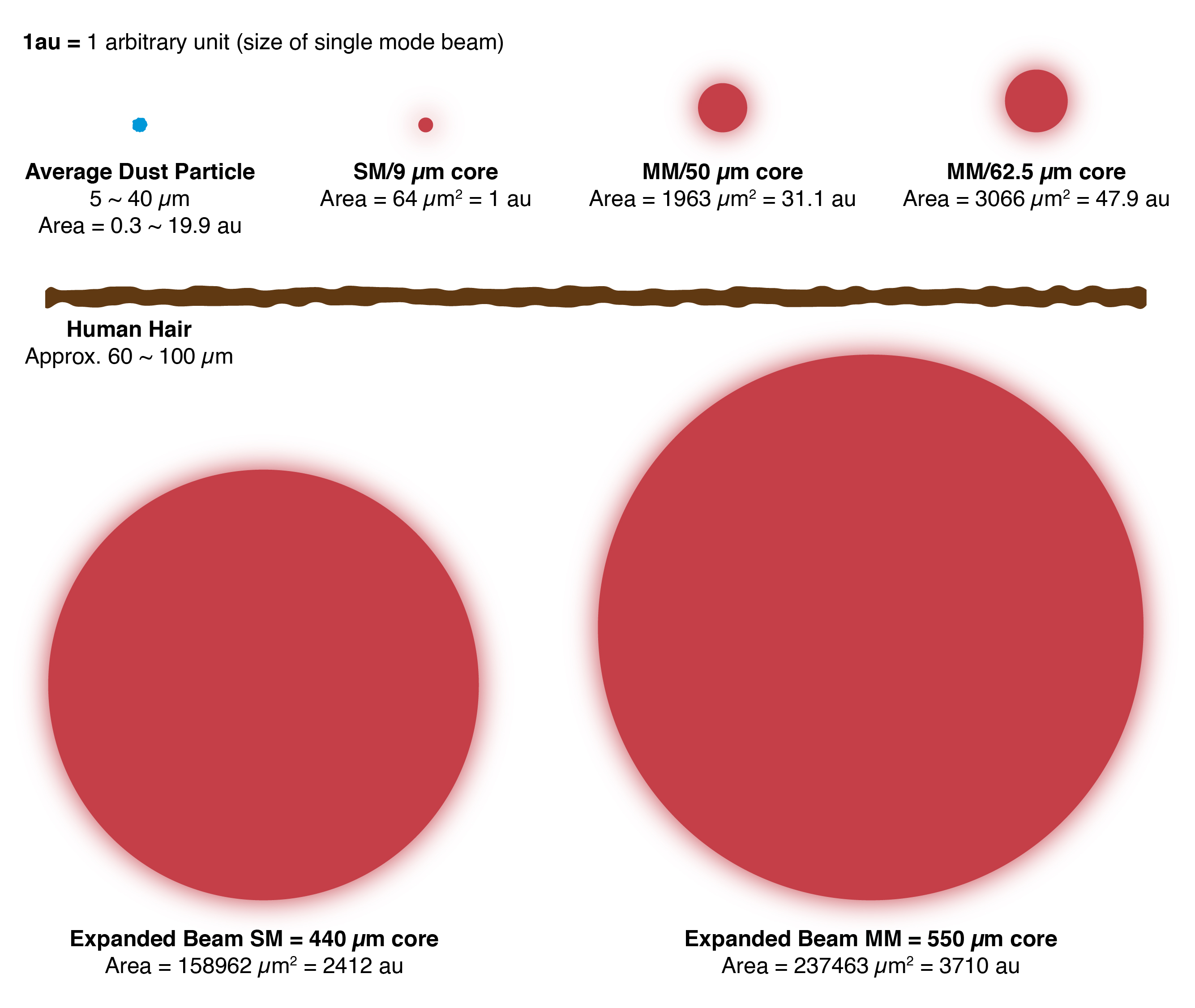
THE EXPANDED BEAM CONNECTOR INSERT
Multi-channel expanded beam connector inserts have been developed to offer a practical method of packaging the expanded beam technology. Typical expanded beam inserts comprise a stainless metal housing containing 1 to 16 spherical lenses (optical channels).
The Fibreco expanded beam insert utilizes a unique, patented optical arrangement whereby the critical interface between the optical fiber and the lens is permanently sealed in a controlled atmosphere during manufacture. This ensures that no dust, moisture, or other contaminants can migrate into the optical path during the product life.
The front face of the expanded beam insert typically has a mating surface, an alignment pin and socket and one or more spherical lenses which are epoxy sealed. The lenses have an extremely hard anti-reflection coating. The Fibreco expanded beam insert has been carefully designed to avoid “dirt traps” and the largely flat front surfaces facilitate easy cleaning. Where ease of cleaning and low maintenance schedules are required, the addition of a window can be specified on some connector inserts to create a flush mating surface for swift and easy cleaning. Anti-reflection coatings are also applied to these windows to minimize back reflection.
Image 1. Fibreco Mini, Junior, Senior and Maxi expanded beam inserts (left), Fibreco expanded beam termination ferrule (right).
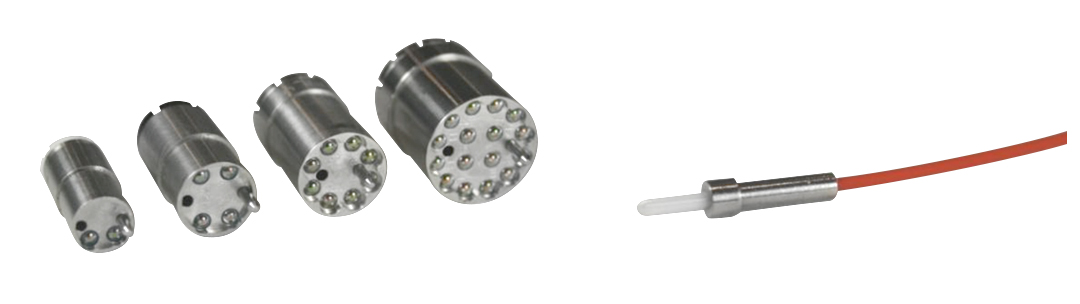
The expanded beam insert is spring loaded when assembled in a connector shell. When two connectors are mated, the expanded beam inserts are aligned by the pin and socket arrangement and contact under spring pressure on their mating faces. The spherical lenses or mating windows do not contact.
Fibreco expanded beam inserts are easily terminated with standard fiber optic termination tools and equipment.
Termination is based on standard LC connector technology (Ø1.25mm) and is terminated onto optical fiber cable using the industry standard epoxy / polish technique. The termini are then simply inserted into the rear of the expanded beam insert and fixed in place with a retainer.
The termini can easily be removed from the expanded beam insert for connector re-use or repair. Importantly, should the expanded beam insert be damaged in service the connector can be repaired by replacing the expanded beam insert without the need for re-termination.
THE EXPANDED BEAM TERMINI
In addition to complete inserts containing the expanded beam components, Cinch also provides, through its GigaCom Interconnect EBOSA™ technology, the ability to provide individual expanded beam termini in popular form factors such as MIL-PRF-29504/4 and /5, and also ARINC 801, in both multimode and singlemode. EBOSA™ (expanded beam optical sub-assembly) provides all the expanded beam benefits highlighted in this document, but with the flexibility to integrate the termini into many more connector forms or custom designs. EBOSA™ also incorporates very easy termination and end face preparation by utilizing standard LC ferrules on the prepared and terminated end. The EBOSA™ then simply screws together and is then inserted into the required connector.
Image 2. Example of expanded beam termini in MILDTL- 38999 SIII connector (left). Example of expanded beam termini in D-Sub and backplane connectors (right).
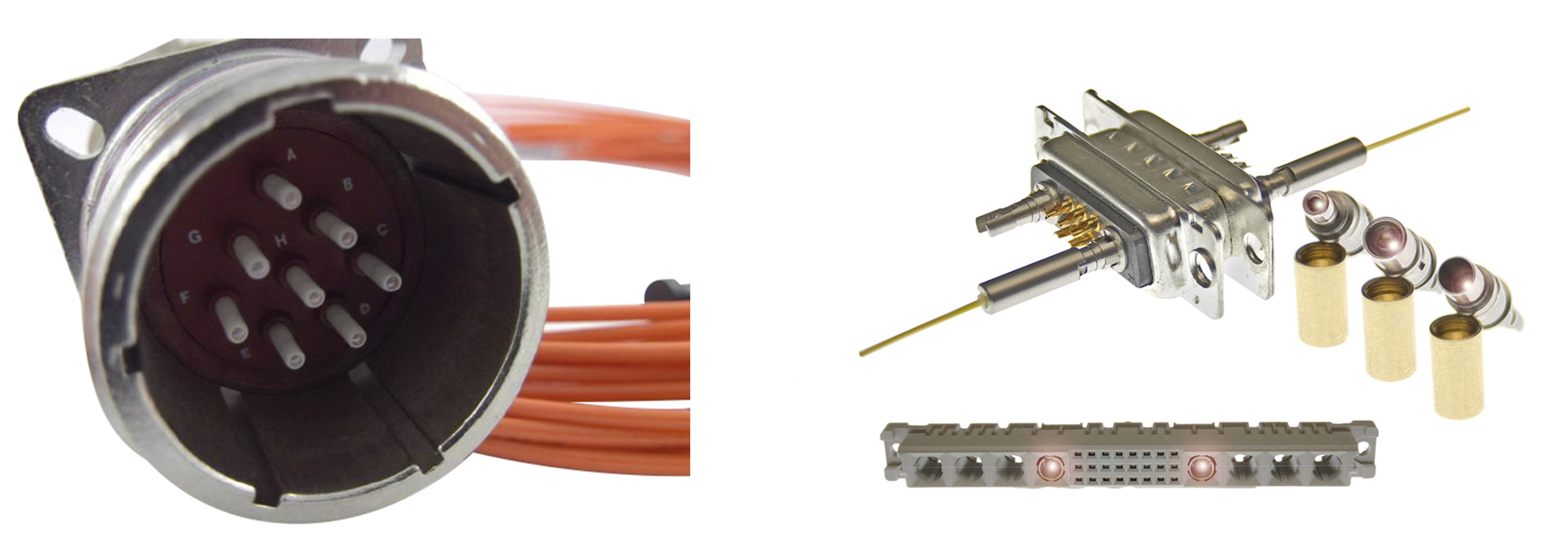
MULTI-CHANNEL EXPANDED BEAM CONNECTOR SHELLS
Hermaphroditic type expanded beam connectors have been designed specifically for external harsh environment applications and are widely used in military tactical communications, outside broadcast, mining, offshore and many other industrial applications. Cable assemblies with hermaphroditic connectors can be easily daisy-chained and there is no requirement for male / female adaptors.
Image 3. Expanded beam solutions
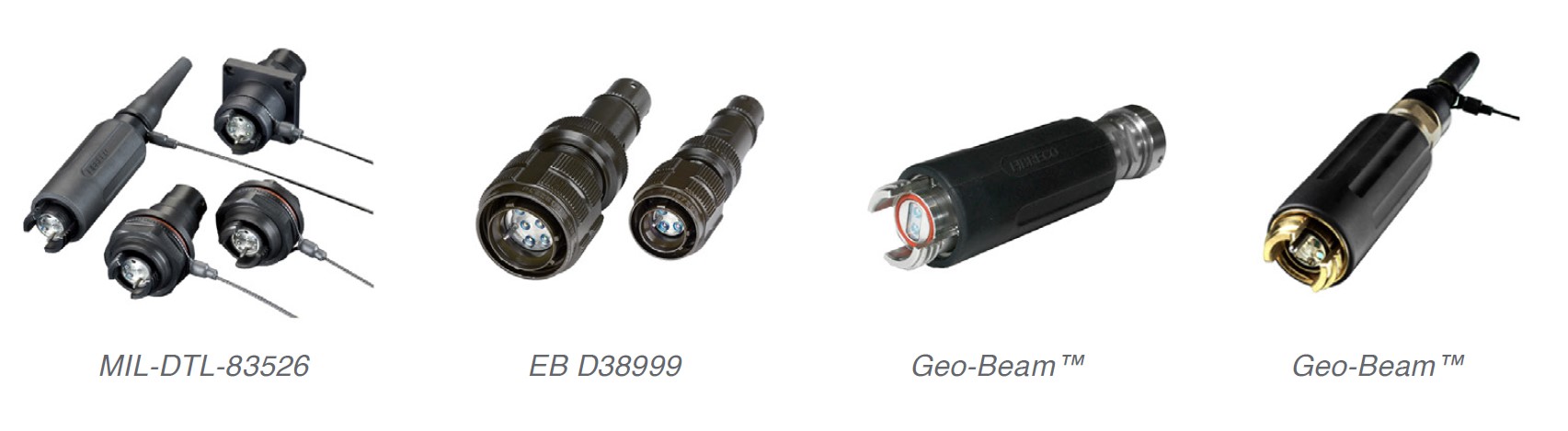
HIGH RELIABILITY IN EXTREME ENVIRONMENTS
While the connector shell design and the quality of the harness manufacture have an important bearing on the reliability of a harsh environment fiber optic connector, by far the most critical factor is its fundamental ability to withstand the harsh environment conditions both when the connector is mated (or with its protective cap fitted), and also in its un-mated and therefore un-protected state.
Physical contact connectors must also withstand the cleaning process as often damage can occur if untrained personnel attempt to clean the connector or incorrect cleaning materials are used. In contrast, expanded beam connectors do not require disassembly or any special tools or cleaning materials to properly clean the connector and damage cannot occur from the cleaning process.
RELIABLE FIBER OPTICS FOR HARSH ENVIRONMENTS
Physical contact connectors are not well-suited for use in harsh environments. They are susceptible to contamination, difficult to clean, and not well water sealed. Additionally, their optical performance will degrade over time in harsh environments.
Expanded beam connectors have been shown to withstand extreme environments without the need for special servicing or cleaning equipment. Protecting the optical fibers behind lenses ensures that no damage or degradation can occur.
The non-contact design of the optical surfaces in expanded beam connectors results in higher insertion loss than physical contact connectors (multimode typically -0.7dB, single-mode typically -1.0dB). However, the optical performance of expanded beam connectors is constant throughout the product life and the likelihood of product failure at a critical point is greatly reduced.
If you are looking for a reliable and low-maintenance fiber optic connection solution for a harsh environment, expanded beam connectors are the ideal choice.
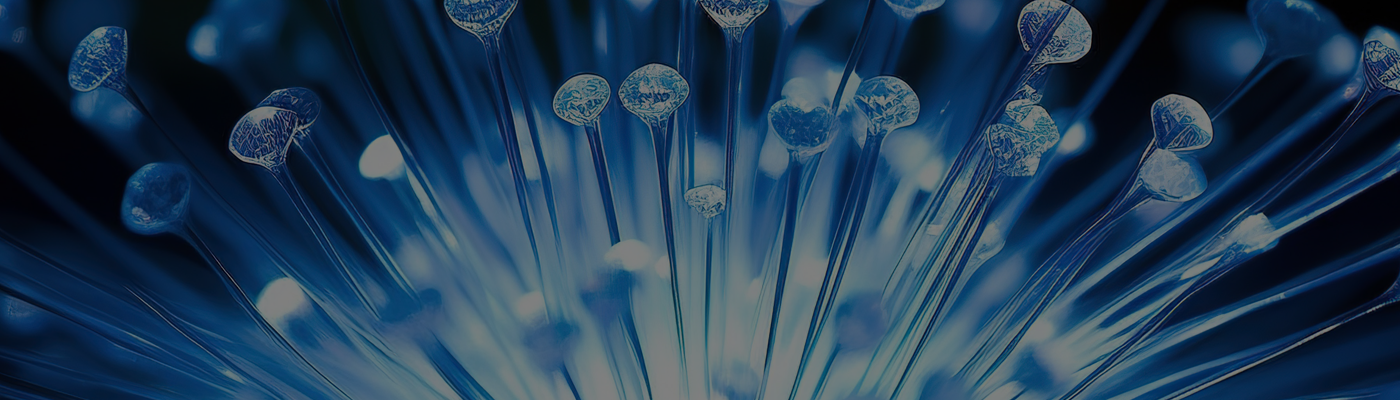
Learn More About the Range of Expanded Beam Connection Technologies
Learn More