BEYOND PROCESSORS: THE IMPORTANCE OF POWER SUPPLIES
The first thing that supercomputer architects think about when building more powerful machines unquestionably is the nature and number of processors and processor cores that their new machines will integrate. There are less heralded innovations required to support leaps in supercomputer performance, of course. Power supplies designed to provide ever increasing efficiency and power density are critical to support advances in supercomputing and high-performance computing (HPC).
RACK POWER DENSITY IS STEADILY INCREASING
A growing number of companies are relying on supercomputing and HPC to process ever-growing pools of data. These companies are increasingly using artificial intelligence (AI) and machine learning (ML) to extract insights that can be used for competitive advantage. The demand for more processing power is insatiable. Satisfying that demand is almost always predicated on increasing the number of processors and processing cores. Supercomputers already consume large amounts of electrical power – and they already expend considerable amounts of heat. Of course, adding processors increases power consumption as well as the amount of heat dissipated.
Figure 1. Average rack power density over time
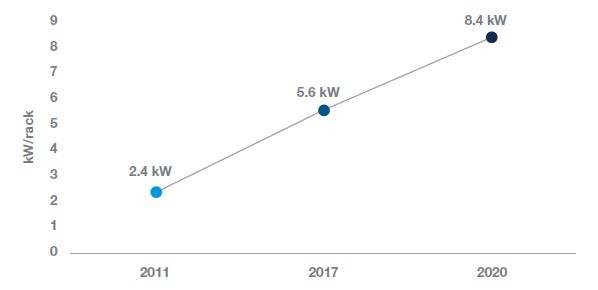
According to a 2020 survey by Uptime Institute, the average server rack power density has increased by 3.5x over the last 10 years to 8.4 kW per rack (see Figure 1), and 10% of applications now exceed 30 kW per rack (Uptime.com 2020). This increase in power density not only requires highly efficient power supplies to mitigate heat output, but often requires application specific customizations to optimize performance and increase reliability.
MODIFIED STANDARD PRODUCTS REDUCE DEVELOPMENT TIME
A suitable power supply does not have to be a fully custom design. Custom designs take time and money to develop and achieving top tier efficiencies and performance is not easy. Often the more effective solution to this challenge is to modify an existing standard product that’s performance has been proven. An in-house company like Bel Power Solutions can deliver quick turn engineering samples of modified standard products to meet specific application requirements.
The discussion below covers Bel’s in-house modification solutions of rack-ready front-end titanium and platinum rated power supplies with customized mechanical features, electrical performance, and firmware/PROM programming.
Discover Bel's TET3600 Front-End Series
View Product VideoEFFICIENCY IS CRITICAL IN HIGH PERFORMANCE APPLICATIONS
As rack power density increases so does the importance of power supply efficiency. When the system is powered on and using electricity, the PSU converts the AC (alternating current) supply to DC (direct current) power. The catch, though, is that power is consumed by the power supply in the process. This is where the efficiency rating comes in. Efficiency is the ratio of the output power supplied to the load versus the input power that is supplied to the PSU (equation 1.), and the difference between those two values is the amount of power that will be dissipated as heat inside the PSU (equation 2.).
Equation 1.
Efficiency [%] = x 100
Equation 2.
Power Dissipation [W] = Input power [W] - Output Power [W]
The internal circuit design and components determine how much power will be dissipated by the PSU. A lower efficiency indicates that more power is being consumed by the PSU internally and therefore producing more heat. This heat must be removed from the system, which often adds cost and space to the system design.
Front end power supplies from Bel Power Solutions provide industry-leading efficiencies and power density. Standard products are all designed to meet Titanium (TET) or Platinum (PFE) level efficiencies as defined by the 80-PLUS program. This gives designers a broad range of efficient options to use as a base model for a customized solution.
80 PLUS CERTIFICATION PROGRAM
To get the full picture of a power supply’s efficiency performance, more than one data point is needed. Power supplies do not spend their entire useful lives operating at 100% load; in fact, it is more typical to operate towards the middle or low end of the power rating. For this reason, it is important to measure the efficiency at several different power levels.
The voluntary 80 PLUS certification program takes loading into account and categorizes power supplies based on their efficiency across several specified load conditions. When first developed in 2004, the program had one tier and required a minimum of 80% efficiency at 20%, 50%, and 100% load at 115 Vac input. Since then, more tiers have been added and are identified by familiar elemental metals (see table 1.). In addition to the efficiency levels, there are also product categories that have their own specific limits for each level and include industrial supplies, internal redundant supplies and power supplies that operate off 380 Vdc inputs.
Table 1. 80-PLUS levels and requirements for 230Vac internal redundant power supplies
Efficiency Level | 10% load | 20% load | 50% load | 100% load | Power Factor min at 50% load |
Bronze | N/A | 81% | 85% | 81% | 0.9 |
Silver | N/A | 85% | 89% | 85% | 0.9 |
Gold | N/A | 88% | 92% | 88% | 0.9 |
Platinum | N/A | 90% | 94% | 91% | 0.95 |
Titanium | 90% | 94% | 96% | 91% | 0.95 @ 20% load |
At the high-end of the ratings are the 80 Plus Platinum and Titanium ratings. A supercomputer or high-performance computing application likely requires a Platinum-rated PSU at minimum. Platinum power supplies’ push the minimum efficiency to 90% or greater at all tested load conditions and increases the required power factor from 0.9 to 0.95. Titanium pushes the limits even further by not only increasing the efficiency limits at 20% and 50% load, but also adds a 10% load requirement and reduces the load at which the power supply must maintain a 0.95 power factor to 20%.
THE BENEFITS OF TITANIUM EFFICIENCY FOR HIGH-POWERED COMPUTING AND DATA CENTERS
As the amount of power demanded from supercomputer, datacenter, and HPC applications increases, so does the benefit from top tier Titanium efficiencies. The 1-2% difference between Platinum and Titanium rating may not seem like a lot, however for many of the applications that front end PSU’s power, every fraction of a percent matters.
Figure 2. 80-Plus Platinum and Titanium performance level badges
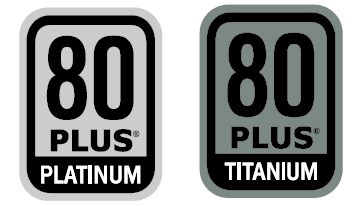
For example, a 2 kW application operating at 50% load, the resulting power dissipation is 63.8 W for Platinum and 41.6 W for Titanium. The 22.2 W difference represents a 35% decrease in power dissipation when switching from a Platinum rated supply to a Titanium. For datacenters that house hundreds or thousands of racks, the cost savings can quickly add up. Table 2 provides an example of the cost savings that can be realized by switching from Platinum to Titanium rated power supplies. This has led Bel to focus their industry-leading expertise on the development of Titanium rated front end power supplies.
Table 2. Example cost difference between Platinum and Titanium efficiency levels
2 kW Power Supply Operating at 50% load (1 kW) | Platinum | Titanium | Titanium – Platinum Savings |
Efficiency | 94% | 96% | 2% |
Power Loss | 63.8 W | 41.6 W | 22.2 W |
Annual Energy Loss | 559 kWh | 364 kWh | 195 kWh |
Annual Energy Usage | 9319 kWh | 9125 kWh | 195 kWh |
Annual Energy Bill @ $0.12/kWh | $1,118 | $1,095 | $23 |
Annual Cost of Energy with 40 Servers per Rack | $44,720 | $43,800 | $920 |
Annual Cost of Energy for Datacenter with 1000 Racks | $44,720,000 | $43,800,000 | $920,000 |
BEL SUPPORTS A WIDE RANGE OF MODIFICATIONS TO STANDARD PRODUCTS
With the broadest range of front-end power supplies in the market, Bel front-ends employ the latest integrated circuits (IC’s) available to provide industry-leading efficiencies and power density. But achieving the highest efficiencies is not the only requirement of leading-edge applications. These applications tend to have unique and application specific requirements that cannot be found off the shelf and often lead to the need for customizations.
Figure 3. TET1500 Block Diagram
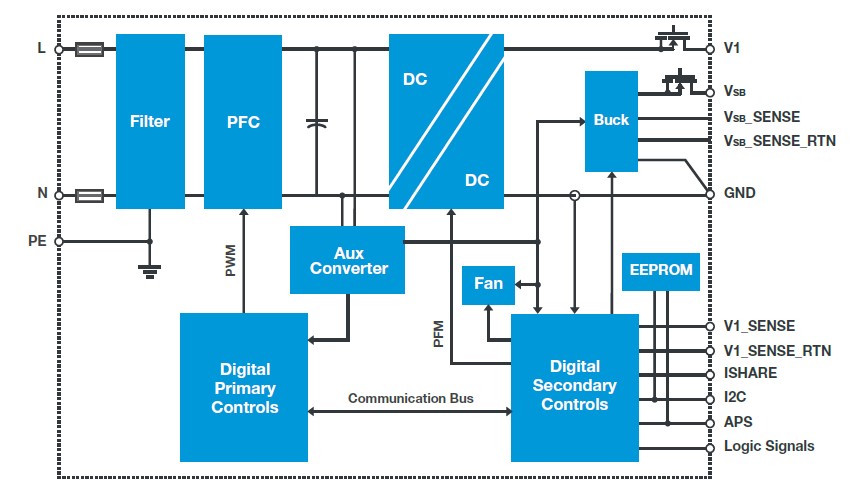
To make these top-tier power supplies accessible to those applications with special requirements, engineers at Bel have utilized their broad product portfolio of industry leading designs, along with their in-house proto-typing capabilities, to develop an efficient process for modifying existing designs to meet specific customer needs. Bel’s team of experts can modify any of their many standard products to quickly produce engineering samples for testing and qualification. These capabilities reduce development time and reduce risk involved with developing fully custom designs.
Let Bel Design Your Custom Solution
See the PossibilitiesMECHANICAL MODIFICATIONS
Many common modifications have nothing to do with electrical performance. These modifications can be as simple as a color change to match a brand standard or other equipment in the rack. Modification could also include the addition of front bezels or adjustments to the mechanical size or shape to fit into unique form factors.
Revising a device’s appearance is easily achievable so the end user can mix and match other products in the rack (Figure 4). Bel also accommodates customer-specific Input and Output connectors, mechanical keying, specific part numbering, and specific packaging. As an option, Bel will meet mechanic-specific sizes for unique applications.
Figure 4. Physical modifications can quickly become a part of shippable products. A selection of Bel's front end power supplies
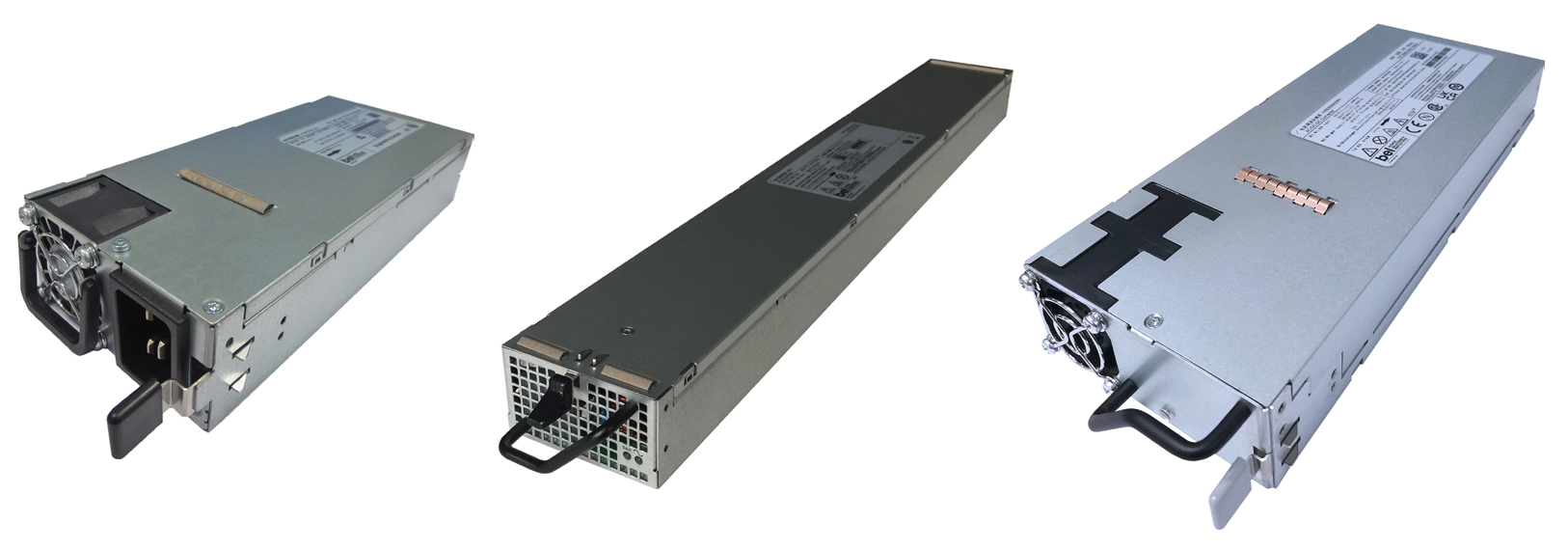
HIGH-BACK PRESSURE APPLICATIONS
Modifications can also service high-back pressure applications. When operating in real systems, PSU users can impact the PSU cooling. This occurs as the system fan(s) compete with the PSU cooling, high-resistance air entry, or exhaust. This reduces the net airflow through the PSU, creating an expensive “backpressure” problem. At the beginning of the design, one must understand the power supply, airflow quantity requirement, and how this may impact the final application operation.
ELECTRICAL PERFORMANCE MODIFICATIONS
Other potential modifications to a standard model include changes to electrical specifications, such as output voltage set-point, output current limit, holdup time, and peak power. The operating temperature may also be extended for applications operating in less controlled environments.
It can be difficult to achieve peak performance with off the shelf power supplies. The advanced digital control of Bel’s front-ends enables them to adjust key specifications to optimize it for specific applications. Items such as the choice of output voltage depends on many factors and can significantly affect system performance. Off the shelf power supplies are typically limited to a few discrete voltage options. To avoid settling for a sub-optimal voltage, Bel’s engineers can quickly modify the setpoint voltage of an existing standard product to help achieve optimal system performance.
In more advanced applications, a custom output voltage may not be enough to achieve the desired performance. For these applications, the output voltage may be further optimized by measuring and adjusting the voltage of individual units during manufacturing. This allows the output voltage to be set precisely under specific load conditions. For example, setting the output voltage to 12V +/- 0.05V at half load as opposed to the normal setpoint accuracy of 12V +/- 0.12V.
In some cases, a modified power supply can help save space by avoiding the use of an over-sized power supply due to high peak power demand. Many applications have high peak loads that occur infrequently. The specification of some power supplies allows for brief durations of output power that is significantly higher than the rated power. Typically, there are well defined limits to the period and duty ratio of these peak power events, which Bel can tailor to the needs of the end system. Without this feature a much larger power supply, that is rated for continuous operation at peak loads, would be needed.
Figure 5. Example of power boost characteristics
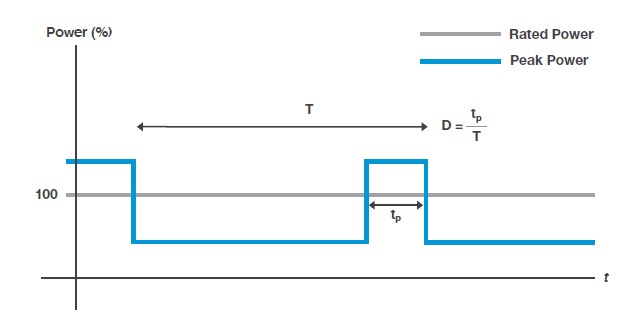
Other modifications can help ensure reliable operation. Protection features, such as over current protection, may be adjusted to satisfy specific application requirements and ensure that the power supply is protected during a fault and does not trip too soon or too late for the given application.
If a fault does occur, and input power is lost, it is important for many applications that the output stay regulated for a certain amount of time while the system switches over to a backup source. This time, known as hold-up time, can also be used to back up critical data. Modification of the hold-up time may be necessary to guarantee continued operation during a fault based on specific system response times.
Figure 6. Example hold-up time waveforms
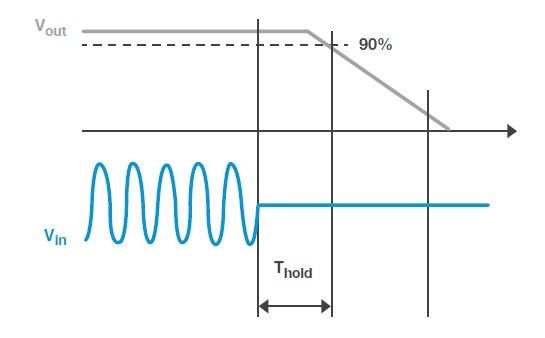
FIRMWARE/PROM MODIFICATIONS
In addition to storing device settings in firmware, these power supplies also contain programmable read-only memory (PROM). The PROM may be used to store customer and/or application specific information to be accessed during operation. These and other modification options can be quickly applied to Bel’s extensive list of existing and proven designs without the time or risk involved with a ground-up custom design.
BEL POWER SOLUTIONS: TAILORED PRODUCTS AND SERVICES FOR DIVERSE INDUSTRIES
Bel Power Solutions offer a comprehensive portfolio of products for different applications, such as for the storage, networking, industrial, and telecommunications industries, and board mount power to system-level architectures for servers. To meet these application requirements, Bel Power Solutions offer the capability to modify mechanical, electrical performance, and firmware/PROM to order. Additionally, Bel’s engineering team offers a broad range of modeling, test, and certification services to expedite the product’s time to market. All of these features significantly increase the product’s competitive advantage.
View Bel’s Full Line of Products for Front-End Power Supplies
View Products