Electromagnetic noise is pervasive. It is the result of electric currents, magnetic fields, and electromagnetic fields. Practically, that means noise is created by such natural phenomena as lightning and solar flares, and manmade electrical or electronic devices like radio transmitters and switching power supplies.
The management of noise in electronic systems is an important part of any initial design because minimizing noise after the design is done or a prototype built is progressively more difficult and expensive. A first step toward the management of noise is to understand the vocabulary, the origins, and the effects of noise.
Noise in Power System Design
In the context of power system design, noise - commonly referred to as electromagnetic interference (EMI) or Radio Frequency Interference (RFI) - appears as unwanted currents. These unwanted currents degrade the performance of any susceptible device. The mechanisms of these unwanted currents are discussed from both the offending source and the susceptible receptor. Electromagnetic Compatibility (EMC) is the ability of the source and the receptor to operate in a given electromagnetic environment.
Types of Emissions
Conducted Emissions
Electric currents flowing from the power supply input to the voltage source are called conducted emissions, see Figure 1.
Figure 1: Typical electronic package.

Conducted emissions are generated at the input (AC or DC) by a current flow in a wire or trace in two ways: differential mode noise and common mode noise (Figure 2). Differential mode noise is measured between two conductors. Common mode noise is present on each of the input conductors and travels to earth. Conducted emissions are superimposed on the input current supplying the power from the voltage source (AC or DC). They may be leaving or entering the power supply.
Figure 2: Typical EMI paths.
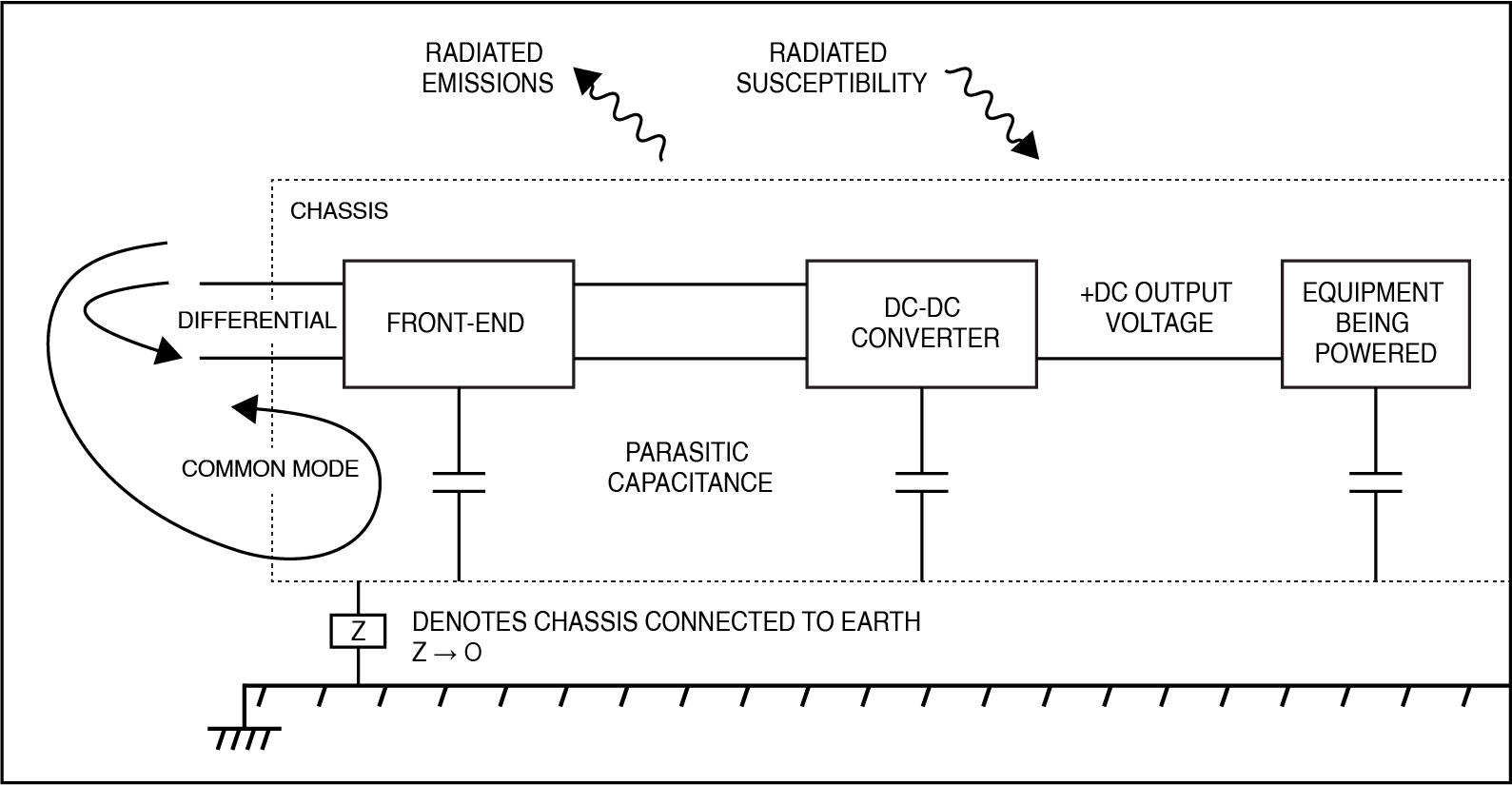
If currents are leaving the power supply and travel to the input voltage source, these are generally known as conducted emissions. If a noise-sourced current is superimposed on the input current and flows into the power supply, this is known as conducted susceptibility. On occasion, one will encounter requirements for “conducted susceptibility,” which is the response of a device to unwanted signals applied to the power leads. Conducted susceptibility specifications are common in military applications.
Another unwanted current, on the output side, is superimposed on the DC output feeding current to the load (s): output ripple current. Usually, any specification for this is based on the particular equipment being powered and as such does not involve any third-party standard.
Radiated Emissions
Radiated EMI refers to an electromagnetic wave leaving or entering the enclosure that houses the product. If electromagnetic waves leave the enclosure, they are known as radiated emissions. If electromagnetic waves are imposed on the product, they are known as radiated susceptibility. Radiated susceptibility is the equipment response to unwanted radiation applied to the enclosure.
Ripple Voltage
There is a fourth area of noise current, but usually not for specification since it is not visible to the end user of the equipment. When the input is an AC voltage, the rectification to create a DC level requires capacitors for energy storage. The DC level on the capacitors will have an AC ripple superimposed on them. This “ripple voltage” will depend on the capacitance value, line frequency, and power level among other factors. It is rare for this to be included in a product specification. This ripple (for a single phase voltage, it is twice the line frequency) may be a measurable component added to the DC-DC converter switching frequency output voltage ripple.
The three types of noise are all caused by devices being turned on and off. After the AC input, rectification takes place in the front end to establish a DC level. Rectification is performed by diodes with the diode’s output feeding capacitance. The diodes are turning on and off with each AC cycle. When the diodes turn off, they do so in < 1 usec, creating switching currents, not only at multiples of the line frequency, but also in the MHz region. These currents will conduct back to the AC input creating part of the conducted emissions spectrum.
There are additional switching elements in the downstream DC-DC converter(s). It is typically from a switching MOSFET(s) on the converter’s primary side and rectifying diodes (or MOSFETs) on the secondary side. The devices here will typically turn on and off in < 20 nsec. The frequencies of the currents can be easily up to 30 MHz. This is the maximum frequency specified in the commercial standards for measuring conducted interference.
If power factor correction circuitry is also included in the front end, there will be additional currents due to the PFC circuitry’s switching MOSFETs and diodes.
Managing Noise Currents
The DC output(s) will also have high frequency switching currents going to the load. The currents going back to the input as well as the currents going to the load can find many conduction paths due to parasitic capacitance within the power supply and the equipment itself. With devices turning on and off at the speeds mentioned, any pair of parallel wires, mechanical mounts, or component mounting will form a parasitic capacitance, and giving high-frequency currents a conduction path, even if the capacitance is only a few pico Farads.
There are also parasitic inductances due to wiring and PCB traces. All lead lengths are inductive and will contribute to inductive kicks (voltages) that will find capacitive conduction paths as well.
Since the currents on the input and output wiring vary with time, they generate electromagnetic waves. This radiated interference may cause undesirable effects on nearby circuitry or equipment. FCC and European test specifications measure this interference with an antenna / receiver combination 10 meters away.
Grounding and Noise Mitigation
Proper grounding will minimize the effects of all noise sources by giving the currents a low-impedance path to earth. There are four places in a power system that are of concern, see Figure 3. Whether the input is AC or DC, points 1,2, 3, and 4 are not the same. The front end input and output (points 1 and 2) will be different potentials due to interconnect resistance and inductive components used for filtering. The DC-DC converter input and output (points 2 and 3) will be different due to the use of an isolation transformer.
Figure 3: Grounding.
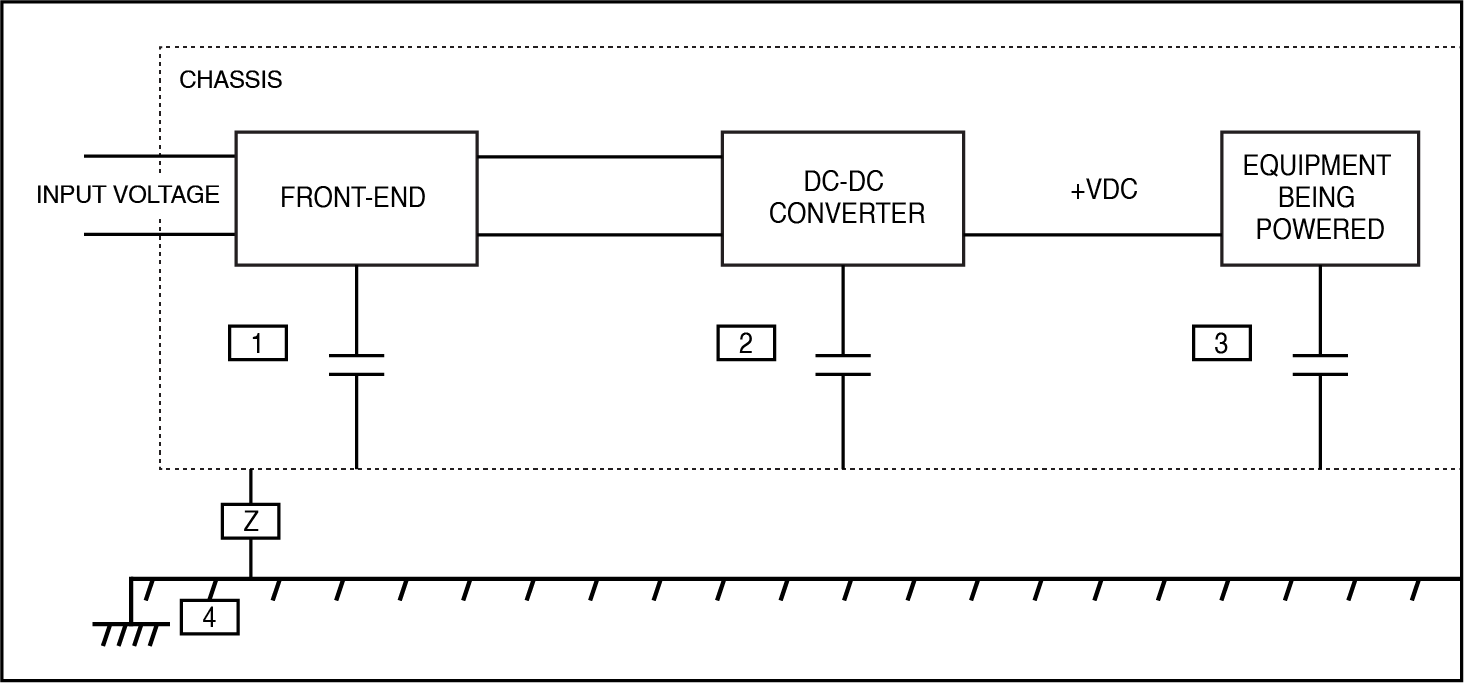
Usually, only the chassis (point 4) is connected to ground (earth). The chassis ground connection is best when Z → 0. It may be useful to look at a block diagram of the system and decide on which paths the high frequency noise currents are likely to take based on how these points are selected and how their connections are implemented.
Using Z = 0, any noise current going to the chassis will wind up traveling to earth. This is the main goal. An example of an undesirable alternate path would be the noise currents traveling from the front end to the equipment being powered and causing a change in behavior. In addition, when going through EMI qualification testing, it is desired that all noise currents go to earth and not to the measuring equipment, as it would effect both differential and common mode noise measurements.
Ensuring EMC Compliance
Compliance to conducted and radiated emissions is usually required by a third party specification, see Figure 4. Conducted emissions have three specifications in use: FCC part 15, Level A or level B in the United States; EN 55032, which replaced EN 55022 level A or Level B in Europe; MIL-STD-461 for military applications (Figure 4). Notice the differences in the low frequency area.
The FCC starts at 450 kHz, the EN 55032 starts at 150 kHz. MIL STD 461, not shown, starts at 10 kHz for CE 102.
Figure 4: Conducted Emission Limits - LISN method.
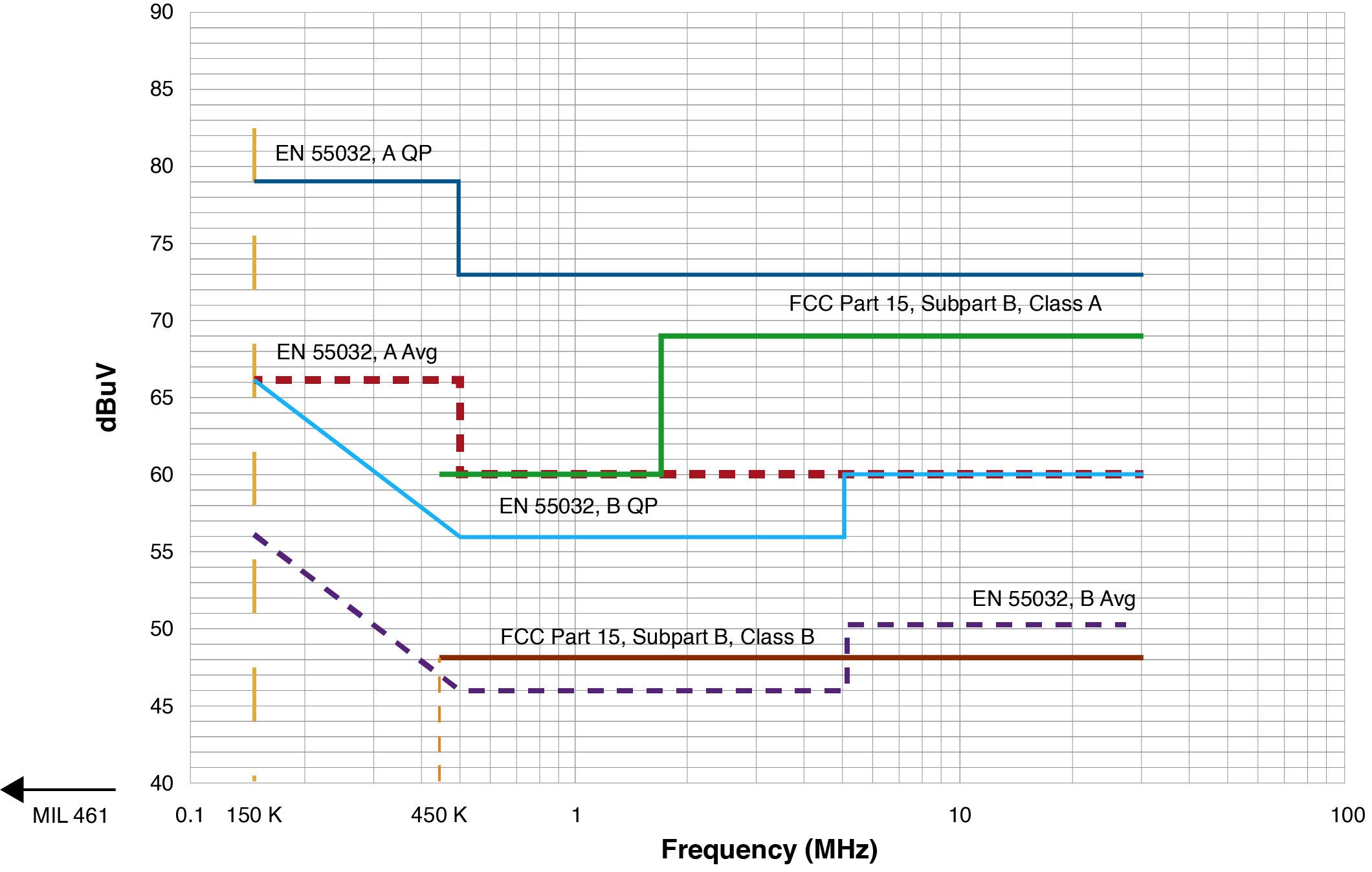
It is a good idea for the designer to verify the revision levels of the specifications of interest and state them in any specification.
Two measurement procedures are in use for conducted emissions: quasi peak and average. The spec limits for each are noted as part of the EN 55032 specification. One or both measurements may be required. Finally, there are two levels shown for the FCC and EN specifications: Level B, if needed, requires additional attenuation in comparison to level A.
The output ripple voltage is usually specified as a percentage of the output voltage and expressed in millivolts peak to peak. A scope bandwidth of 20 MHz is standard practice for measurement of this parameter.
Electromagnetic radiation usually emanates from the input and/or the output cable. This is because the cables are exposed. The power supply and the electronics inside the package will, most likely, have electromagnetic waves attenuated prior to leaving the enclosure.
View Bel's selection of AC-DC and DC-DC power supplies
Learn More